
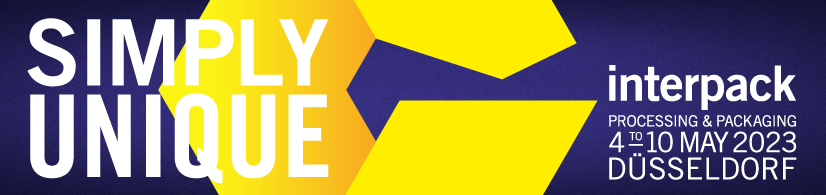
Beccles, UK – 27th April 2023.
Bradman Lake to launch new high-speed Intelligent Motion Feeder at Interpack 2023
Visit stand no. 5C22 Hall 5 at Interpack 2023 on 4th-10th May at the Messe Düsseldorf Trade Fair Centre, Germany and see our new IMF Intelligent Motion Feeder (IMF) connected to our Flow Wrapper and Top Load Cartoning System. PLEASE REGISTER HERE
Designed to increase efficiency and flexibility, the new IMF automatically feeds products into the FT120 Flow Wrapper. The wrapped products then enter the DRT Dual Racetrack Robotic Toploader, which will pick and place products into cartons formed and glued on the HSS Servo Driven Carton Former. Filled cartons will transfer to the IL120 Carton Closer and are sealed using hot melt adhesive, demonstrating a flexible and modular top load cartoning approach.
For the side load approach, Bradman Lake will display the well-established SL903 End Load Cartoner which erects, loads, and closes cartons within one frame. A wide range of optional features, including a low-height carton hopper, are available to enable the machine to be readily adapted to meet the customer’s specific requirements.
The exhibit will demonstrate Bradman Lake’s capabilities and experience in providing both top load and side load packaging approaches. Both lines can be easily integrated with one of the Bradman Lake’s case packers and palletisers for a complete packaging system – From Process to Pallet – making Bradman Lake the obvious single-source supplier.
Bradman Lake packaging equipment sets the benchmark for primary, secondary and tertiary packaging. Equipment can be supplied as a ‘stand-alone’ machine for low speed, hand-fed applications, or as a fully automatic system to meet the demands of the most sophisticated hi-tech processing and packaging lines. They have become the machines of choice for many multinational manufacturers operating in the bakery & biscuit, chocolate & confectionery, dry foods, chilled & frozen foods, pharmaceutical, and healthcare industries.
Equipment on display key features and benefits:
The Top Load Packaging system includes:
IMF Intelligent Motion Feeder, with Integrated Layer Collator – New Development
Incorporates the latest Bradman Lake’s transfer technology. New servo-driven linear guided pockets that accept a randomly spaced stream of products and transfer each product into the infeed of the flow wrapper, negating the need for traditional feeders. This delivers excellent access for the end user, the option of constant or indexing motion on the same machine and greater flexibility in handling a wide range of products and collations.
High speed, up to 600 products per minute.
Greater tolerance to product positioning, for higher packaging efficiency.
Rapid changeover, no tools required, which increases productivity.
Easy cleaning with no mechanisms below the product line for greater sanitation.
Small footprint, new frame style, and full-height doors for ease of access.
The machine incorporates several other great features that will be launched and demonstrated by our Team at the show.
FT120 Flow Wrapper
Operates at the highest level of efficiency and seal integrity, even for challenging heat-seal applications.
New and improved ‘backward compatible’ flow wrap sealing technologies. Simple conversion parts or modular replacements can enable the flow wrapper to run recyclable, biodegradable, paper and single substrate mono materials.
Robust end crimp sealing module that provides hot or cold seal options.
Quick changeover takes less than 15 minutes and requires only a single operator. It is simple to operate and maintain as well as being able to accommodate a wide range of product sizes.
Soft Jaw. Unique to Bradman Lake, it prevents misplaced products from jamming in the end seal jaws.
Reel to Reel Splicing. Automatic splicing is a standard feature on a system. A manual splice is also available for stand-alone machines.
Automatic Web Tracking. Maintains position of wrapping material presentation from the reel, providing increased efficiency and productivity whilst keeping material width to a minimum.
Discharge Top Control. It provides a consistent transfer onto the discharge conveyor, therefore, ensuring a regular pitch between products when interfacing with downstream equipment.
No Gap No Crimp. If no gap is detected between products on the infeed, the end seal jaws will not come together, and a long bag is formed that is rejected on the machine infeed. The machine does not stop production.
No Product No Bag. If no product is detected in the machine pitch, the end seal jaws simply wait for the next product. No empty pack is produced, so there is no wastage and the machine continues to run.
High Speed. Machine versions capable of wrapping speeds up to 1200 packs per minute are available.
HSS Servo Carton Erector
Provides consistent carton erecting which is critical for the efficient operation of a top load cartoning system.
The HSS machine utilises a servo-powered reciprocating ‘shuttle’ method of feeding the carton blanks into the forming tool. This guarantees excellent performance with quick and easy setup using factory set tooling.
Flexibility to erect cartons and trays using hot melt glue or four corner lock on the same machine.
Tooling Flexibility. The machine can erect a wide range of board types including chip board and corrugated board. It can be tooled to erect different styles of lock and glue form cartons with types ranging from standard three flap or front flap cartons, turn-over-end cartons, to hooded lid cartons, as well as shelf-ready display style cartons that include atypical shapes associated with seasonal products.
It incorporates advanced techniques and factory set change parts that allows quick and repeatable changeovers and requires only a single operator.
DRT Robotic Pick and Place Top Loader
The machine employs state-of-the-art technology in all functions. The Dual Racetrack (DRT) comprises two pairs of servo-driven transmission belts with two trains of product specific pockets attached. The servo-driven vacuum infeed includes product reject.
Incorporates an intelligent belt technology carton management system of servo-driven side belts that accurately spaces pre-formed cartons, trays or cases and consistently transfers them at high speed to the robotic loading station.
The DRT is equipped with an individual product detection and reject system to ensure carton count is as specified.
Ultimate flexibility. The DRT robotic pick and place top loader can be set up to provide dual loading functionality for customers needing the ability to automatically collate and load flow wrapped products into a choice of either a paper board carton, rigid retail case or the infeed of a multipack flow wrapper.
Light weight, precision end of arm tooling (EOAT). Advanced design end-of-arm tooling techniques to pick and place products into cartons, trays, or cases so that different layer collation patterns can be created.
Misaligned and out of position product is automatically rejected ensuring high operating efficiencies.
Size changing can be achieved in minutes, requires few change parts and is consistent with virtually instant repeatability without the need for engineer intervention.
IL120 Carton Closer
Tool-less size changeovers can be accomplished quickly and easily which significantly reduces downtime and increases productivity for customers that run several different carton sizes.
Uses unique ‘Flexible Carton Control’ (FCC) technology that allows for cartons containing products of inconsistent size, protruding above the carton base, to be closed without jamming.
Overhead FCC conveyors can be fitted with servo motor driven automatic lift and descend. This feature provides excellent operator access from all sides of the machine and facilitates rapid size change.
The End Load packaging equipment includes:
SL903 End Load Cartoner:
Great flexibility to handle a variety of products and carton designs. It is designed to handle a wide range of cartons and products, including lower grade carton materials, with easy, fast and repeatable size changing. It can be supplied to run a multitude of profile shaped cartons including gable ends, turnover end, simple folds, and creases thus allowing the carton to hold and nest the product reducing, and in some cases, eliminating the use of internal acetate trays.
Simple, yet robust, stainless-steel construction makes the machine ideally suited to the food, pharmaceutical and health care industries.
A variety of product infeed and collating systems are available for total automation with upstream and downstream equipment.
We are looking forward to seeing you there!
Features and benefits of the Bradman Lake product range:
Experience. Bradman Lake has a large installed base; our customers benefit from over 75 years of knowledge in designing and building packaging equipment. Bradman Lake is an established brand with a high reputation for machine reliability and value for money worldwide. Its position as an innovative, progressive and forward-thinking global supplier of packaging solutions derives from vast industry experience, a consultative, customer driven approach, delivering commercially viable solutions with strong project management and a commendable health and safety record.
All Bradman Lake products are the result of thoroughgoing research and development and are developed from an undertaking that every project, no matter how small or technically challenging, will be a custom solution to meet exact customer requirements. This responsive, solutions-based approach has helped establish Bradman Lake as a leading global provider of future-proof packaging technology.
Flexibility, “Future Proof” Principal. The ergonomic modular design provides the ultimate flexibility to handle a wide range of products, carton formats and sizes that can be rapidly adapted to specific requirements enabling our customers to easily meet the demands of the fast-changing markets at any time in the future.
Sustainability. Environmental sustainability is an important focus for Bradman Lake, both in machine development and business operation. As well as promoting recycled packaging, it seeks to minimise packaging material waste through various equipment features. Ergonomic equipment design enables concurrent task completion in one compact frame, reducing spatial requirements, lowering energy and air consumption while ensuring no harmful emissions are produced.
Bradman Lake is proud to communicate its machinery helps to remove many millions of single use plastic trays year on year!
Safety and Hygiene. Robust and well-built to the latest safety and hygiene standards. Upgradable machine construction to handle wash-down applications that are required in the food and healthcare industries. Machine guarding has been designed to provide operator safety, maximum visibility of operation and excellent machine access.
From Process to Pallet. Bradman Lake provides true, single-source turnkey systems, with project management from initial concept to site acceptance and beyond. The benefits to customers include commonality of engineering standards and parts; a single servo motor size, common wiring patterns and identical HMI look-and-feel all contribute to ease of use and operation; a single point of contact for procurement; project manager and aftermarket; FAT for full system occurs in single location and systems are fully integrated and tested prior to delivery resulting in expedited start up.
Intuitive HMIs and a common control platform offer customers an easier method of extracting information from a single source, as well as seamless exchange of data upstream and downstream. A single network infrastructure offers unprecedented levels of visibility, flexibility and scalability to respond to market opportunities and operational threats.
Initial Capital Savings. The core competence of the equipment is its unique capability for seamless future integration with other Bradman Lake innovative equipment to achieve full automation and yet retain initial capital savings.
Smart Layout. Compact footprint which is available in several orientations to suit plant layout and incorporates narrow integral electrical cabinets with easy access. All machines are designed with minimum frame sizes and easy-access guard design.
Customer Service: Backed by readily available and award-winning customer support, commercial commitment, resources, and spare parts delivery.
About Bradman Lake
Established in 1948, Bradman Lake provides innovative packaging solutions to an international client base. The company is a leading designer and manufacturer of packing machinery and turnkey systems to the bakery & biscuit, chocolate & confectionery, dry foods, chilled and frozen foods, consumer, pharmaceutical and healthcare sectors. In 2022 the company was awarded the prestigious Queens Award for Enterprise. Bradman Lake’s manufacturing plants are located at Beccles and Bristol in the UK and Rock Hill, SC, in the United States. Bradman Lake is a wholly owned subsidiary of the multi-disciplined UK engineering and manufacturing group, Langley Holdings plc.