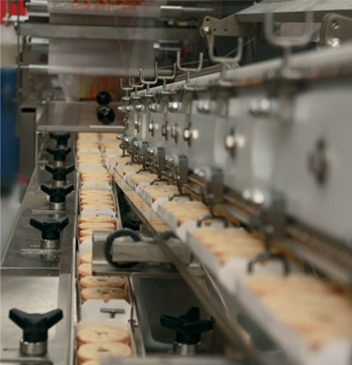
Fully-automatic Feeders / Collators
High volume production lines rightly demand fully automated packaging systems that offer flexibility in operation and are capable of accepting normal irregularities in the product itself and in the product supply rate. With many years of experience in the handling of delicate, sticky, friable, and fractious products, we have developed feeding systems designed to deliver and present your product perfectly to the next stage of the packaging cycle.
A wide range of feeders is available to suit the customer’s requirements.
The Inline Phase Feeder is designed to interface to a horizontal flow wrapper with the product being presented in a narrow edge leading format from either a Bar Turn Unit, Product Orientation Feeder, or an Automatic Distribution System. It is designed to form a queue of products and then phase individual product into the horizontal flow wrapper’s infeed flights.

The Shuttle Phase Feeder is ideal for delicate products, sticky products, or products in trays products where a pressure-less queue is required prior to the phasing section in order to reduce potential damage to the product and minimise rejects.

The AF Angle Feeder is designed to interface with an Automatic Distribution System (ADS), or it can be manually presented with products, either directly from the main production Angle Feeder (AF) conveyor or as an off-line machine. The product is presented to the first gap closing belt in a wide edge leading format. The Angle Feeder (AF) then takes the product narrow edge leading and transfers it as an individual or as multiple products into the infeed section of a horizontal flow wrapper.

The Product Orientation Feeder (POF) is available in a variety of widths and lengths, and the number of bases and side belts can be changed to suit the specific application. The POF is designed to accept the products either in regimented rows or randomly distributed on a delivery conveyor and to configure them into a single stream, narrow edge leading.

The Smart Belt (SB) inline automatic infeed receives products at random and uses a series of servo-controlled belts to correct the random position of each product relative to the target pocket of the horizontal flow wrapper’s infeed conveyor. The final transfer is aided by an overhead paddle. The product would normally be presented to the smart belts with the wide edge leading. Right-angle machines are available.
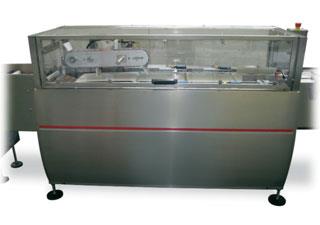
The LC is designed to interface with a product feeder, taking individual products and collating them into single or multiple stacks before flow wrapping on the horizontal flow wrapper.
Product is presented by primary infeed carriers, then positioned onto the various support shelves by a servo-controlled pivoting ramp. When the required collation is achieved, the complete collation(s) is transferred into the main infeed of the horizontal flow wrapper by a servo-controlled overhead transfer. It is possible to run individual products through the unit simply by deactivating the ramp mechanism.

The SBS is designed to interface with a Phase Feeder, taking individual products and collating them into pairs in a “side by side” format, before flow wrapping them on a horizontal flow wrapper.

Bradman Lake has been at the forefront of continuous motion product merging for more demanding, higher speed applications, using twin stacked shuttle phase feeders. The product is collated in a side by side or stacked format without the need for intermittent mechanical motion. The system can be fed by either Bradman Lake’s Automatic Distribution System (ADS) or twin Product Orientation Feeder (POF). Lane balancing is achieved by dynamic speed control and the use of pressure-less product queues which are held within each shuttling system.
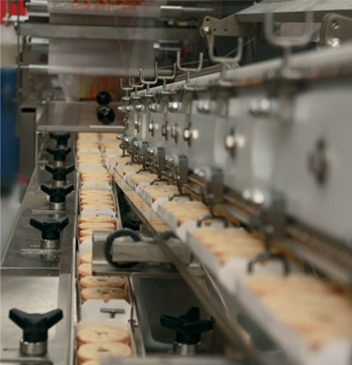
The Cascade Loader comprises a system of infeed conveyors that feed product into a rotary pocket. The machine’s function is to collate single or multiple products and synchronise their placement into the infeed pockets of an automatic horizontal flow wrapper or bagger.
The cascade loader includes an abort system to reject incorrect products.
Single or multiple cascade loaders can be interfaced to a single horizontal wrapper’s infeed or bagger’s infeed.
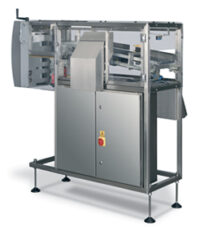
The bowl feeder is designed to interface with the roll wrapper to handle round compressed tablets, dragees, lozenges, chocolate pieces, boiled sweets, pre-wrapped chews and candies, gums and pastilles.
A variety of feed systems, including colour or flavour sequence are available.
